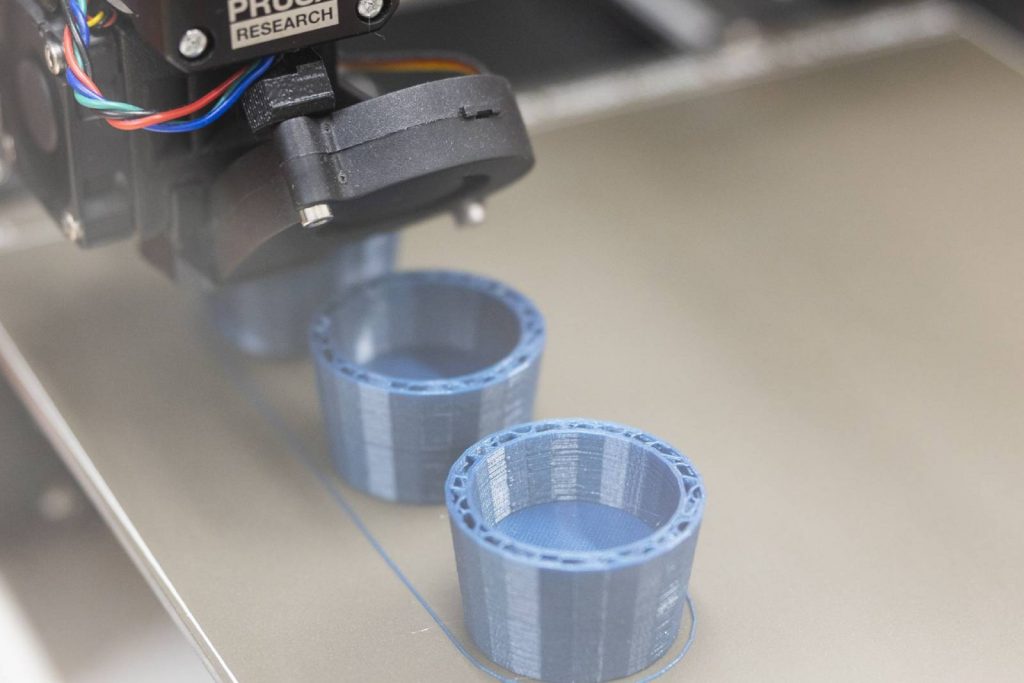
In the realm of manufacturing and production, 3D printing, also known as additive manufacturing, has revolutionized the way we create and design objects. From intricate jewelry to full-scale houses, the possibilities seem endless. But a question that often arises is, How tough is 3D printed stuff? This article aims to delve into the intricacies of 3D printed materials' durability, the factors influencing their strength, and the advancements in technology that are continually enhancing their toughness.
The toughness of 3D printed objects is primarily determined by the material used, the printing process, and the design of the object. Common materials used in 3D printing include plastics like ABS (Acrylonitrile Butadiene Styrene) and PLA (Polylactic Acid), metals such as titanium and stainless steel, and ceramics. The inherent properties of these materials significantly influence the durability of the final product.
For instance, ABS is known for its robustness and resistance to high temperatures, making it suitable for creating durable parts. On the other hand, PLA, a biodegradable material, is less durable but offers higher precision and aesthetic appeal. Metals like titanium and stainless steel are used for their high strength and durability, especially in industries like aerospace and automotive.
The printing process also plays a crucial role in determining the toughness of 3D printed stuff. Techniques like Fused Deposition Modeling (FDM), Selective Laser Sintering (SLS), and Stereolithography (SLA) each have their unique impact on the final product's strength. For example, FDM, which works by depositing layers of molten material, often results in anisotropic materials. This means the material's strength varies depending on the direction of the applied force, usually being weaker along the layers.
In contrast, SLS and SLA, which use lasers to fuse or cure the material, can produce isotropic materials with uniform strength in all directions. However, these processes often require more complex machinery and higher costs.
The design of the object, including its geometry, layer thickness, and the orientation of the print, also influences its toughness. For instance, increasing the layer thickness can enhance the strength but may compromise the object's surface finish and detail.
Advancements in technology are continually improving the toughness of 3D printed materials. New materials with enhanced properties are being developed, and hybrid techniques combining the advantages of different printing processes are emerging. For example, Continuous Fiber Fabrication (CFF) involves embedding continuous fibers into a 3D printed matrix, significantly enhancing the material's strength and stiffness.
In conclusion, the toughness of 3D printed stuff is not a straightforward concept. It is a multifaceted characteristic influenced by various factors, from the material used to the design of the object. As technology continues to advance, we can expect to see even tougher and more durable 3D printed materials in the future. However, it is essential to understand these factors and their interplay to make the most of this revolutionary technology and its potential.