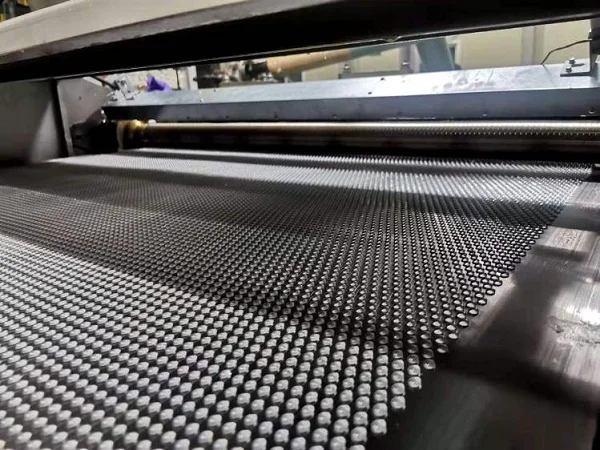
Hot melt adhesives (HMAs) have gained immense popularity in various industries due to their ease of use, fast setting times, and versatility. From packaging and automotive manufacturing to construction and electronics, hot melt adhesives are used to bond various materials effectively. However, the production of these adhesives involves sophisticated processes that ensure consistency, quality, and ease of application. One such crucial piece of equipment in the production of hot melt adhesives is the hot melt adhesive pelletizer. In this article, Little Sky will explore in-depth what a hot melt adhesive pelletizer is and how it works. By understanding the role of this machinery, manufacturers can optimize their production processes, improve the quality of the final product, and contribute to higher efficiency in industrial adhesive applications.
What Is a Hot Melt Adhesive Pelletizer?
A hot melt adhesive pelletizer is a specialized machine designed to transform molten hot melt adhesive into small, uniform pellets. These pellets can then be easily packaged, stored, and transported for use in various industrial applications. The process of pelletizing the adhesive ensures that it is easier to handle, measure, and apply as needed, improving both the efficiency of the manufacturing process and the end-user experience. The primary function of the pelletizer is to cool down the molten adhesive and solidify it into small, consistent-sized pellets. This process is critical for ensuring the correct melt viscosity and adhesive properties once the pellets are re-heated and applied in real-world scenarios. Hot melt adhesive pelletizers are widely used in industries such as packaging, automotive, textiles, and paper manufacturing, where adhesives are required in bulk for bonding materials during production.
How Does a Hot Melt Adhesive Pelletizer Work?
The operation of a hot melt adhesive pelletizer involves several key steps. The machine is designed to handle high temperatures and ensure that the hot melt adhesive is safely cooled and formed into pellets. Here is a breakdown of the working process:
1. Melting of the Adhesive
Before pelletizing can occur, the solid hot melt adhesive (often in blocks, beads, or granules) must be heated to a molten state. The adhesive is placed into a hopper, where it is heated to the desired temperature inside a melt tank or extruder. This heating process is critical because the adhesive needs to reach a specific temperature range to achieve the proper flow and bonding properties. Depending on the composition of the hot melt adhesive (which can include materials like EVA, polyamide, polyurethane, and more), the temperature settings will vary. Most hot melt adhesives melt at temperatures ranging from 150°C to 220°C (302°F to 428°F).
2. Extrusion and Pelletizing Process
Once the adhesive has reached the proper molten state, it is extruded onto the steel belt of the hot melt adhesive pelletizer, which serves as both a conveyor and a cooling surface. The molten adhesive is pushed through a nozzle or die plate, where it is extruded in the form of thin streams or ribbons. These extrusions are deposited onto the steel belt, which continuously moves the material forward. The steel belt plays a critical role in this process, offering a stable, smooth surface for the molten adhesive to cool and solidify. Unlike other pelletizing systems, which may rely on air or water for cooling, the steel belt provides both cooling and transport simultaneously. As the molten adhesive moves across the belt, it begins to solidify, forming a solid surface that is still flexible enough to be cut into pellets. The key advantage of using a steel belt is its ability to maintain even heat distribution and provide a continuous flow of material. The high surface area of the belt allows for efficient heat dissipation, which speeds up the cooling process and helps achieve uniform pellet sizes.
3. Cutting and Pelletizing
After the adhesive has cooled sufficiently and solidified, the next step is to cut it into uniform pellets. In a hot melt adhesive pelletizer, this cutting is typically done using rotating knives, shear blades, or rotary cutters positioned above the steel belt. The speed and precision of the cutting mechanism are crucial to achieving uniform pellet sizes. The cutters are typically configured to ensure that the adhesive ribbons are sliced into small, consistent pellets that are easy to handle and transport. The pellet sizes can vary, depending on the requirements of the end application, but typically range from small beads just a few millimeters in diameter to larger chunks. The pellets need to be uniform in size and shape because inconsistent pellet sizes can affect the melt rate and bonding performance when the adhesive is re-melted for use in production processes. The hot melt adhesive pelletizer ensures this uniformity by precisely controlling the cutting process.
4. Cooling and Collection
Once the adhesive ribbons are cut into pellets, they need to be further cooled before collection. This cooling phase is vital for ensuring that the pellets maintain their shape and do not clump together. The steel belt itself serves as a cooling surface, helping to dissipate the heat from the molten adhesive as it moves along the belt. In some systems, additional cooling mechanisms may be employed, such as air cooling or water sprays. These cooling methods help to speed up the solidification process, ensuring that the pellets are quickly cooled to a temperature where they can be safely handled. Many hot melt adhesive pelletizers are designed with advanced cooling systems that ensure even, rapid cooling. This prevents the adhesive pellets from sticking to each other and helps maintain the consistency of the final product.
5. Collection and Storage
Once the adhesive pellets have cooled and solidified, they are collected in large containers or hoppers positioned beneath the steel belt. From here, the pellets are either sent to packaging systems or transported to storage areas for later use. The collection process can be automated to allow for continuous operation, reducing downtime and improving overall efficiency. At this stage, the pellets are typically in a solid state and can be stored for extended periods without degrading. They are easy to handle, transport, and measure, which is a key advantage of pelletizing hot melt adhesives. In addition, the uniformity of the pellets ensures that they can be accurately measured when re-melted for application in production processes.
The hot melt adhesive pelletizer is a vital machinery in the production of high-quality hot melt adhesives. By converting molten adhesives into small, uniform pellets, pelletizers streamline the manufacturing process, improve the efficiency of adhesive handling, and ensure that adhesives perform consistently across a wide range of industries. From packaging and automotive to textiles, electronics, and construction, the applications of hot melt adhesive pelletizers are broad and varied, making them indispensable for industries that rely on high-quality adhesive bonding. The precision, efficiency, and safety benefits offered by hot melt adhesive pelletizers make them a cornerstone of modern adhesive production, helping manufacturers meet the growing demands for fast, reliable, and effective bonding solutions.
https://www.th-littlesky.com/Hot-Melt-Adhesive-Granulator-Supply.html
www.th-littlesky.com
Little Sky Mechanical Engineering Kabushiki Kaisha