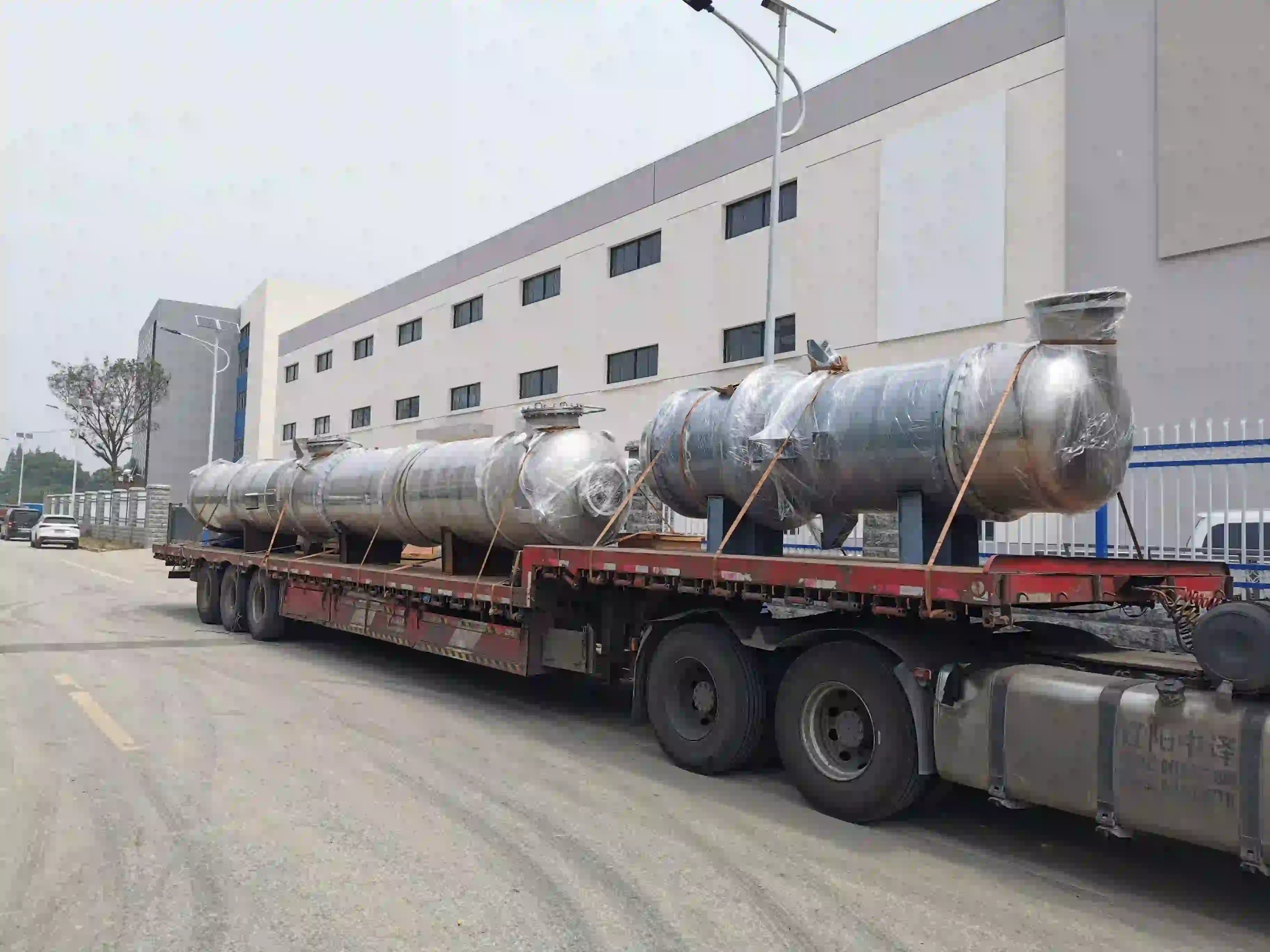
Titanium pressure vessels are rapidly becoming an essential component in various industrial applications due to their superior strength, corrosion resistance, and reliability. These vessels are designed to handle extreme pressures and demanding environments, making them indispensable in industries such as aerospace, chemical processing, and energy production. In this article, Qiwei will delve deeper into the manufacturing processes of titanium pressure vessels.
The Importance of Material Selection in Pressure Vessel Design
The design of pressure vessels requires careful consideration of several factors, including the internal pressure, temperature, and chemical environment the vessel will be exposed to. The material chosen for a pressure vessel directly impacts its performance, longevity, and safety. Titanium, known for its remarkable strength-to-weight ratio, is often the material of choice for high-pressure vessels. Unlike traditional materials like steel, which can corrode and degrade over time, titanium offers exceptional resistance to corrosion, even in harsh environments such as those found in marine, chemical, and high-temperature applications. Its ability to withstand aggressive chemicals, saltwater, and extreme temperatures makes it a reliable and durable material for pressure vessels that need to maintain their integrity under stress. Titanium pressure vessels are favored in industries where high performance is critical and where failure could result in catastrophic consequences. The ability of titanium to maintain its structural integrity even in demanding conditions is one of the key reasons why it is considered a superior choice over other metals.
Manufacturing of Titanium Pressure Vessels
The manufacturing process for titanium pressure vessels is more complex and costly compared to traditional materials like steel or aluminum. This is due to the difficulty in machining titanium and the specialized techniques required to form and weld titanium components.
Material Selection and Preparation
The first step in manufacturing titanium pressure vessels is selecting the appropriate grade of titanium. There are several grades of titanium, with Grade 2 and Grade 5 being the most commonly used for pressure vessels. Grade 2 titanium is commercially pure titanium, known for its excellent corrosion resistance and formability. Grade 5 titanium, also known as Ti-6Al-4V, is an alloy containing aluminum and vanadium, offering higher strength and better heat resistance compared to Grade 2. Once the material is selected, it must be prepared for fabrication. This typically involves cutting the titanium into the required shapes and sizes using precision tools. Due to titanium's toughness, special cutting tools, such as those made from carbide, are used to ensure precise and clean cuts.
Forming and Welding
The next step is the forming of the titanium into the desired shape. Titanium can be formed using various methods, including hot rolling, cold rolling, and forging. These techniques involve applying heat and pressure to the titanium to shape it into the form of a vessel. Due to titanium's high reactivity at elevated temperatures, forming processes must be carefully controlled to prevent contamination or oxidation. Welding is another critical aspect of titanium pressure vessel manufacturing. Titanium welding requires specialized equipment and expertise, as titanium's high reactivity can lead to contamination if not properly shielded. Welding titanium typically involves using an inert gas, such as argon, to protect the weld area from atmospheric contamination. The use of advanced welding techniques like Gas Tungsten Arc Welding (GTAW) ensures strong, clean welds that maintain the integrity of the vessel under pressure.
Quality Control and Testing
Once the titanium pressure vessel is assembled, it undergoes rigorous testing to ensure its strength and reliability. Non-destructive testing methods such as ultrasonic testing, x-ray inspection, and hydrostatic testing are commonly used to check for flaws, cracks, or weaknesses that could compromise the vessel's performance. Hydrostatic testing, which involves filling the vessel with water and applying pressure, is particularly important to simulate real-world conditions and ensure the vessel can safely withstand the required internal pressure. Additionally, post-weld heat treatment may be performed to relieve stresses that may have developed during the welding process. This helps to enhance the mechanical properties of the titanium and ensures the vessel meets the required specifications for strength, ductility, and pressure resistance.
Titanium pressure vessels offer an array of advantages that make them the preferred choice in industries where strength, durability, and reliability are paramount. Their excellent corrosion resistance, high strength-to-weight ratio, and ability to withstand high pressures and temperatures make them ideal for use in critical applications. Although the initial cost of titanium pressure vessels may be higher than other materials, their superior performance and longevity ensure they are a worthwhile investment for industries requiring the highest standards of safety and performance. As industries continue to demand more advanced materials that can withstand increasingly harsh environments, titanium pressure vessels will undoubtedly play an essential role in shaping the future of pressure vessel technology. Their unparalleled combination of strength, resistance, and reliability ensures that they will remain a staple in industries that demand the utmost precision and safety.
https://www.tnztn.com/Titanium-Pressure-Vessel
www.tnztn.com
Wuxi Qiwei Nonferrous Technology Co., Ltd.